Search
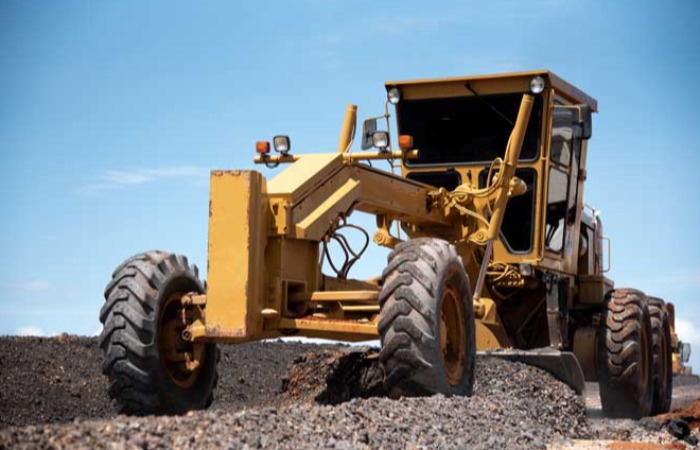
Graders of Tomorrow
Shaping the future of infra, motor graders are evolving with advanced tech and precision to meet the growing demands of tomorrow’s construction landscape.
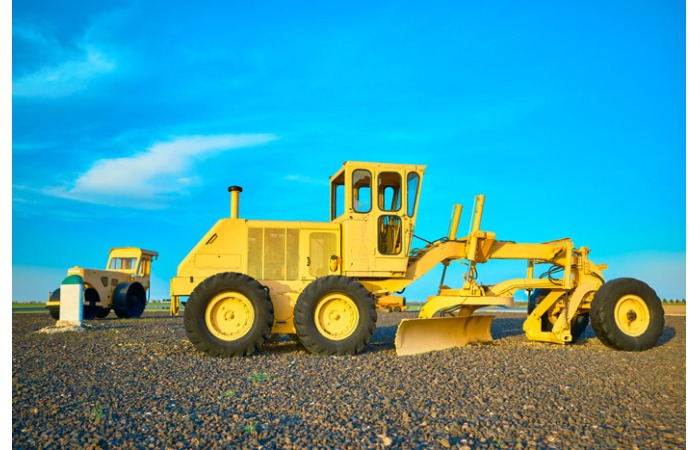
Grading the Future
As the demand for advanced road networks and improved connectivity continues to surge, the clamor for motor graders in the construction industry is reaching unprecedented heights.
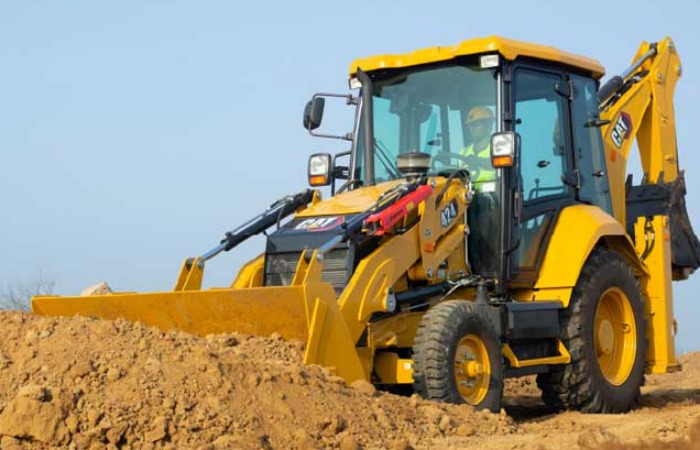
Fuelling the future
Backhoe loader manufacturers are developing hybrid or fully electric backhoe loaders, which significantly reduce or eliminate fuel consumption and emissions.
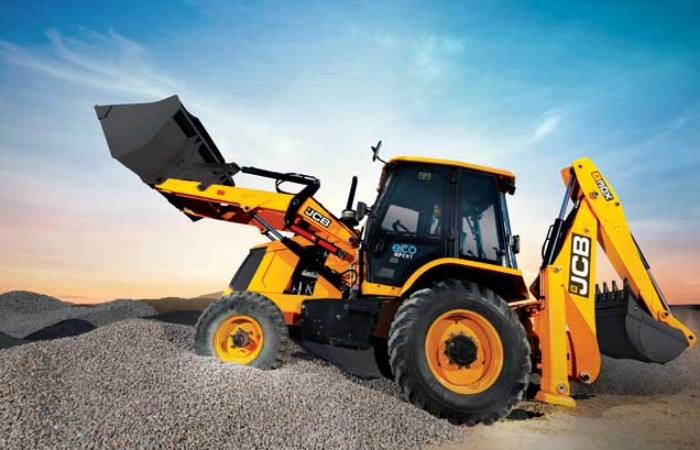
Going forward, digital technology will play a key role
Deepak Shetty, CEO and Managing Director, JCB India, speaks on the key demand drivers for backhoe loaders in India, and its dealership and product service
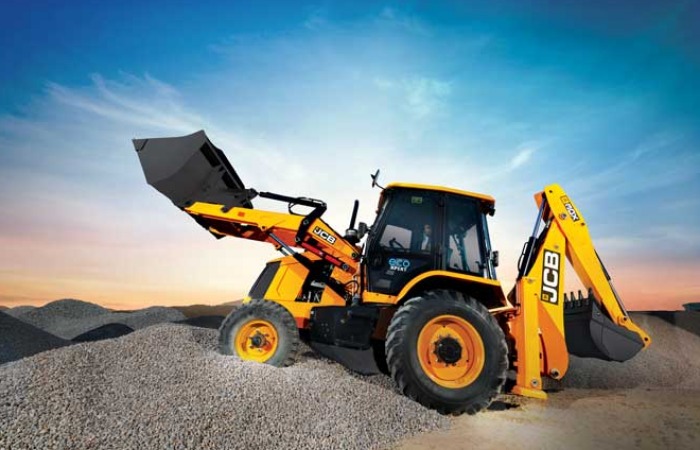
Going forward, digital technology will play a key role
Deepak Shetty, CEO and Managing Director, JCB India, speaks on the key demand drivers for backhoe loaders in India, and its dealership and product service.
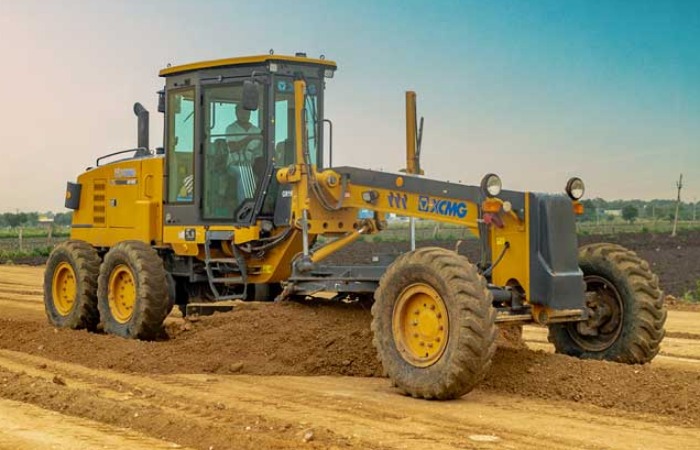
Up-grading roads!
The road construction industry in India is undergoing a paradigm shift. Robust demand, higher investment and significant policy support in the road construction industry are driving the demand for motor graders in India.
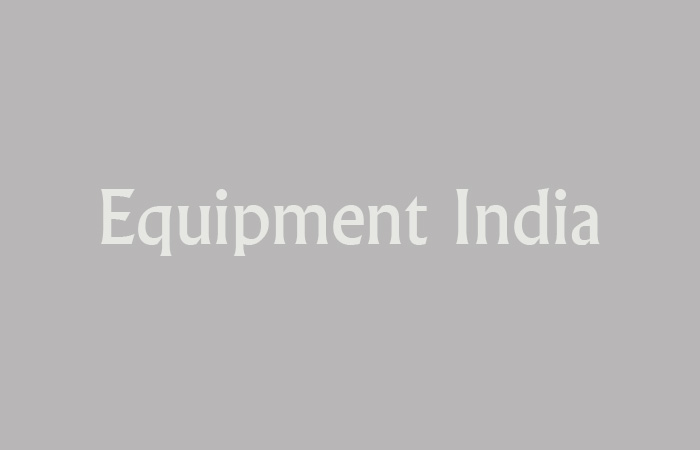
Mahindra launches BS4 backhoe loader with better productivity
Mahindra’s Construction Equipment Division (MCE) has launched its new range of BS4 backhoe loaders called the Mahindra EarthMaster SX. Interestingly, the company is making big claim with the promise of a disruptive customer value proposition.
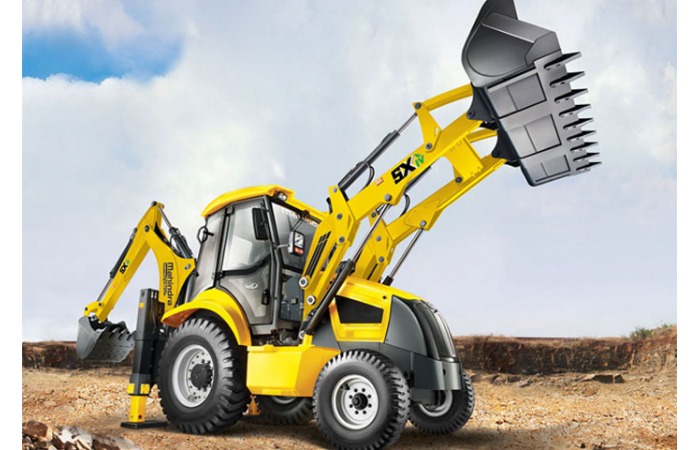
Mahindra launches BS4 backhoe loader with better productivity
Mahindra’s Construction Equipment Division (MCE) has launched its new range of BS4 backhoe loaders called the Mahindra EarthMaster SX. Interestingly, the company is making big claim with the promise of a disruptive customer value proposition
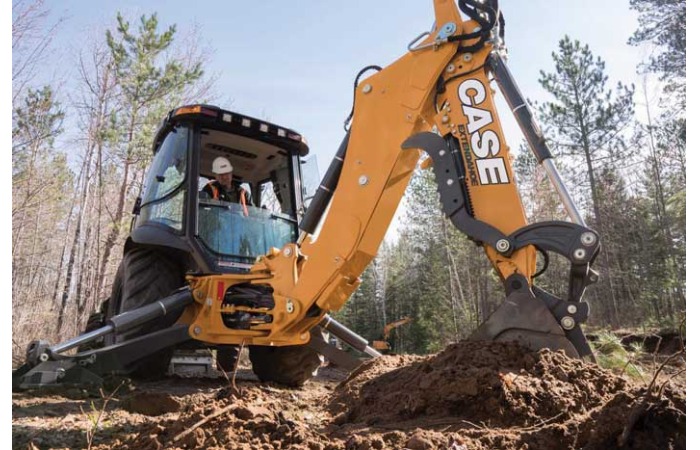
$5.13 Bn Opportunity!
Growing at a CAGR of 9.4 per cent, the Indian backhoe loader market is likely to touch $5.13 billion from $1.77 billion in 2021.
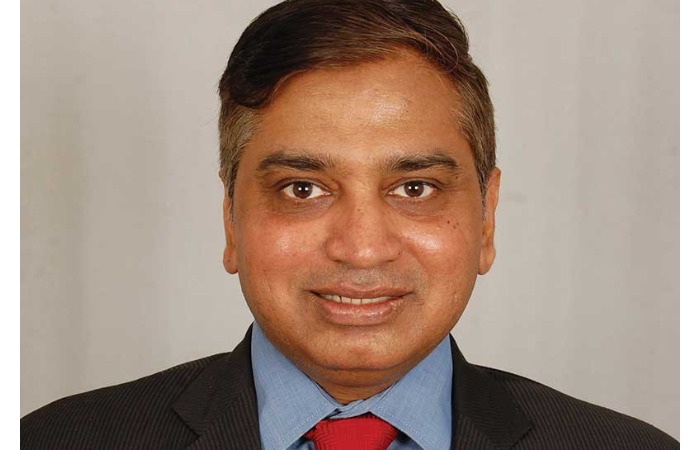
Mahindra launches BS4 backhoe loader with better productivity
The company is guaranteeing the highest productivity per litre in the segment else they will take the machine back. Moreover, an uptime service guarantee is also being offered to customers.
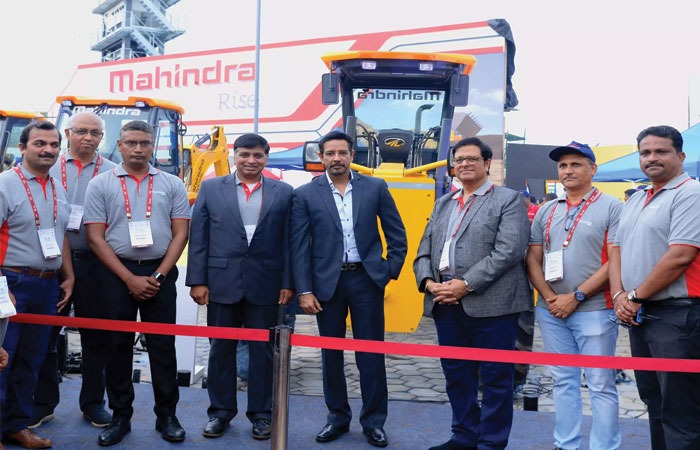
Mahindra unveils ‘G75 Smart’ Motor Grader
Mahindra’s Construction Equipment Division (MCE), a part of the Mahindra Group, announced the expansion of its road construction equipment range with the launch of the brand-new Mahindra RoadMaster G75 Smart – “Profit Ka Partner”.
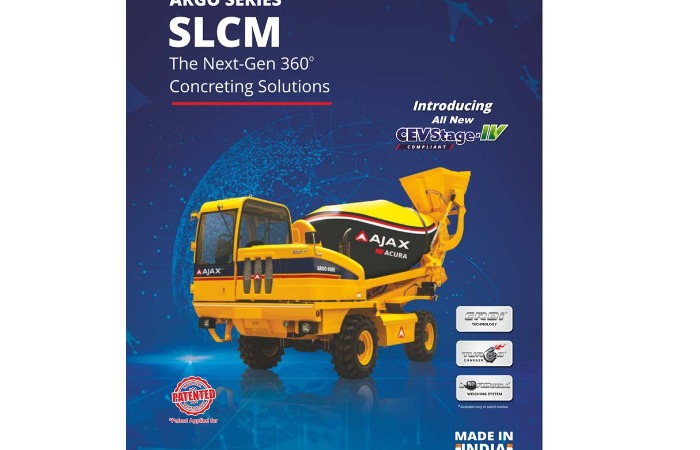
AJAX introduces the ‘All new CEV Stage-IV’ compliant ARGOs
These engines are more environment friendly with well proven CRDi technology and After Treatment System (ATS) that reduces emission levels.
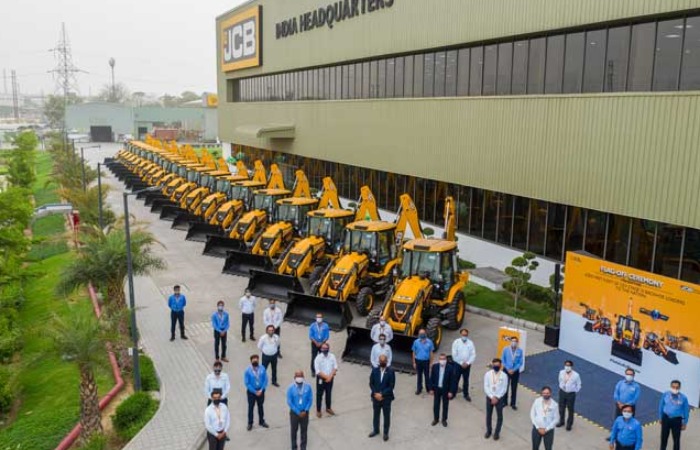
JCB’s range of CEV stage IV backhoe loaders
India’s leading manufacturer of earthmoving and construction equipment, JCB India flagged off its new range of CEV Stage IV backhoe loaders at its Headquarters at Ballabgarh (Delhi-NCR). The range includes the new 3DX Plus, the 3DX Xtra, the 3DX Super and the 4DX to meet a wide range of applications for customers.
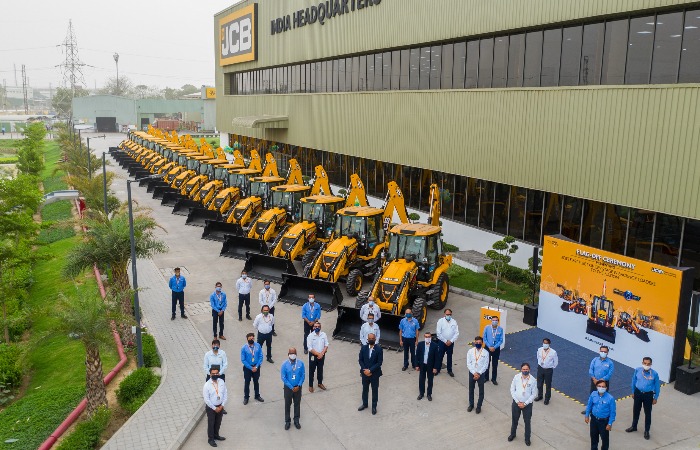
JCB launches its range of CEV stage IV backhoe loaders
The range includes the new 3DX Plus, the 3DX Xtra, the 3DX Super & the 4DX to meet a wide range of applications for customers.
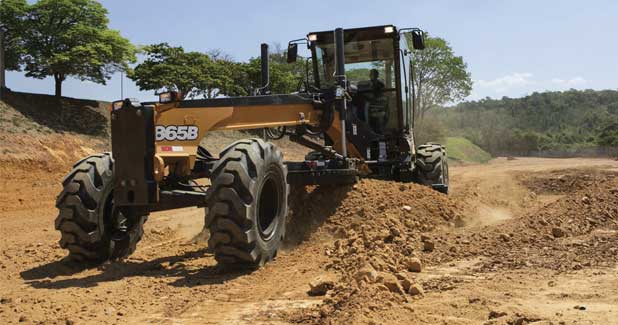
Grading the Future
The current market conditions are tough for motor graders since the projects are not active due to the coronavirus impact.
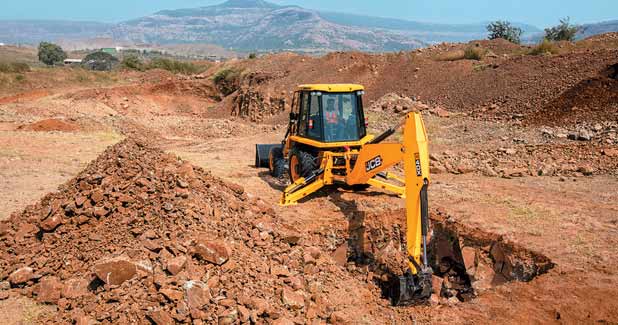
TECH-MOVES
With the government plans to invest Rs 102 trillion in infrastructure development in the next five years, the demand for construction equipment will be immense.
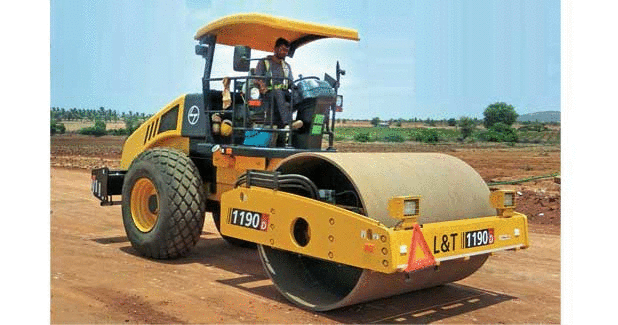
THE ROAD AHEAD
The roads and highways sector is expected to bounce back soon with the government's corrective measures to combat slowdown and the large number of projects planned in the coming years. The road equipment players are bullish on the future growth prospects.
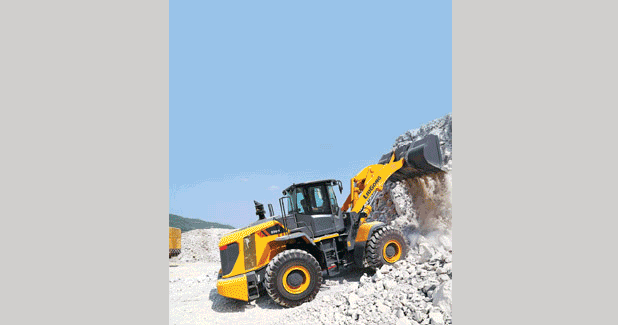
Loads of Opportunities
With the construction activity picking up and mining operations reviving in India, new opportunities are knocking at the doors of the wheel loader market.
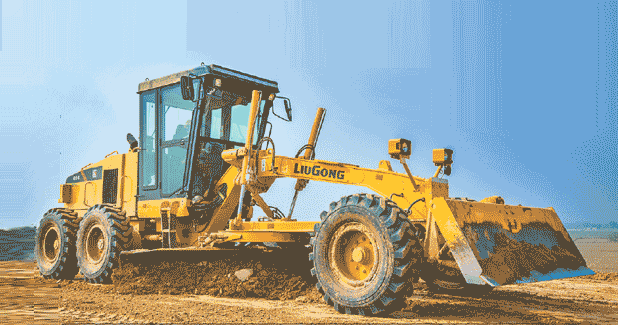
Pushing Growth
Motor grader market has seen growing in the past couple of years with applications spreading into rural road projects as well as in highways.
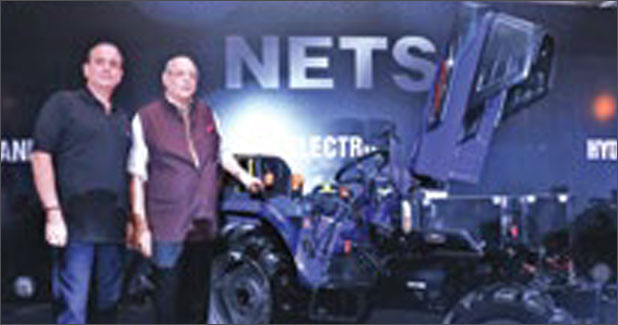
New Tractor Series from Escorts
Escorts launched India's first electric and hydrostatic concept tractor and an expanded global portfolio of tractors for the export and domestic market in 22 HP to 90 HP range under the brands Farmtrac and Powertrac, compliant with tier 4 emission norms of Europe and America amidst 43 international distributors.
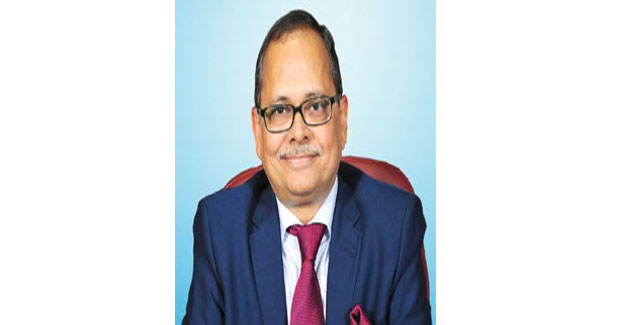
We foresee increased participation from neighbouring countries
Infrastructure sector is one of the key drivers for Indian economy and also constitutes primary market for construction machinery. This sector is mainly responsible for propelling India's overall development and enjoys prime focus from government for policy initiatives.
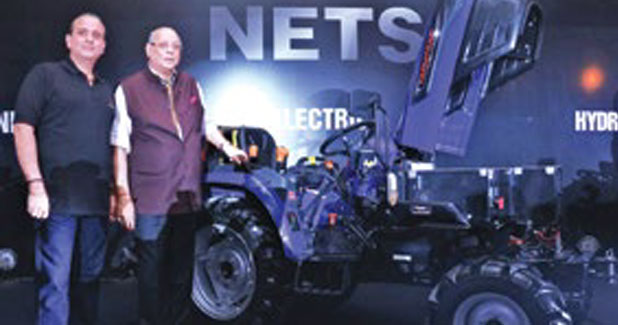
New Escorts Tractor Series
India's first electric and hydrostatic concept tractor and an expanded global portfolio of tractors for the export and domestic market in 22 HP to 90 HP range under the brands Farmtrac and Powertrac, compliant with tier 4 emission norms of Europe and America amidst 43 global distributors.
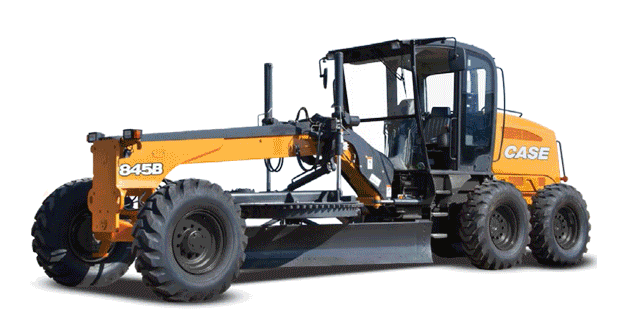
Making rapid strides
Motor graders have seen unprecedented growth in the past couple of years, which is expected to continue in the coming years as well with road projects continue to grow.
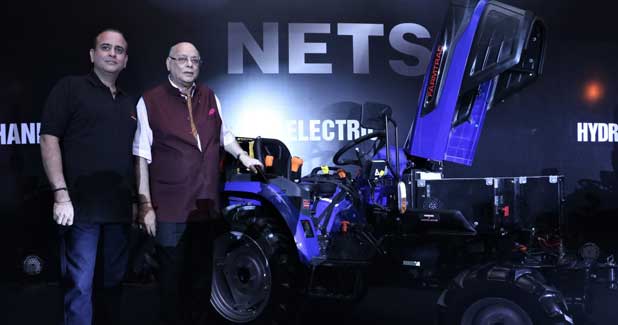
Escorts unveils India?s first electric tractor concept
Escorts Ltd launched India?s first electric and hydrostatic concept tractor and an expanded global portfolio of tractors for the export and domestic market in 22 HP to 90 HP range under the brands Farmtrac and Powertrac, compliant with tier 4 emission norms of Europe and America amidst 43 international distributors.
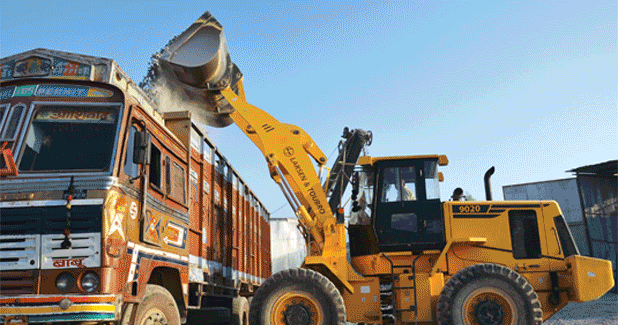
ON THE CLOCK!
Material and earth movements are the major work content of all infrastructure developments and mining activities. Front-end loaders, backhoe loaders, dozers and application-centric equipment as options for the users to choose from to suit individual requirements.
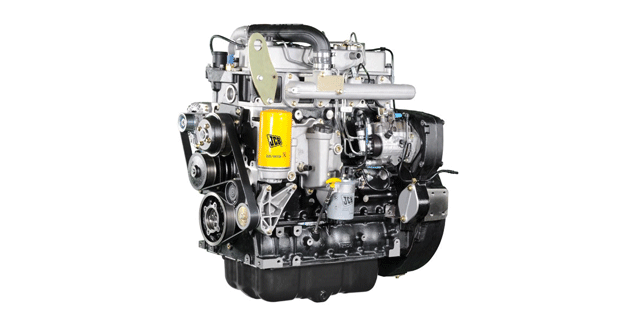
Engines of Future
Latest environmental norms, best fuel efficiency and low OPEX costs, dictate developments of new generation engines. Latest environmental norms, best fuel efficiency and low OPEX costs, dictate developments of new generation engines.
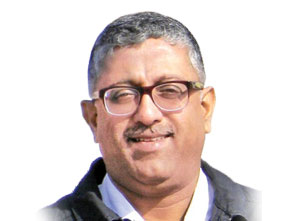
Our products have features that directly boost productivity to the customer.
The LeeBoy 523 is the result of intensive first-hand dialogue with customers and other stakeholders, to not only enhance productivity and operational efficiency, but also deliver a product that surpasses customer expectations. The findings from the customer dialogues enabled us to focus strongly on meeting three key expectations shared by the customer a reliable and rugged product, effective Post Sales Care (PSC) and lower running and maintenance costs. These have been kept in mind at all stages